Our Projects
LNG Peak Shaving Facilities – Cherokee LNG
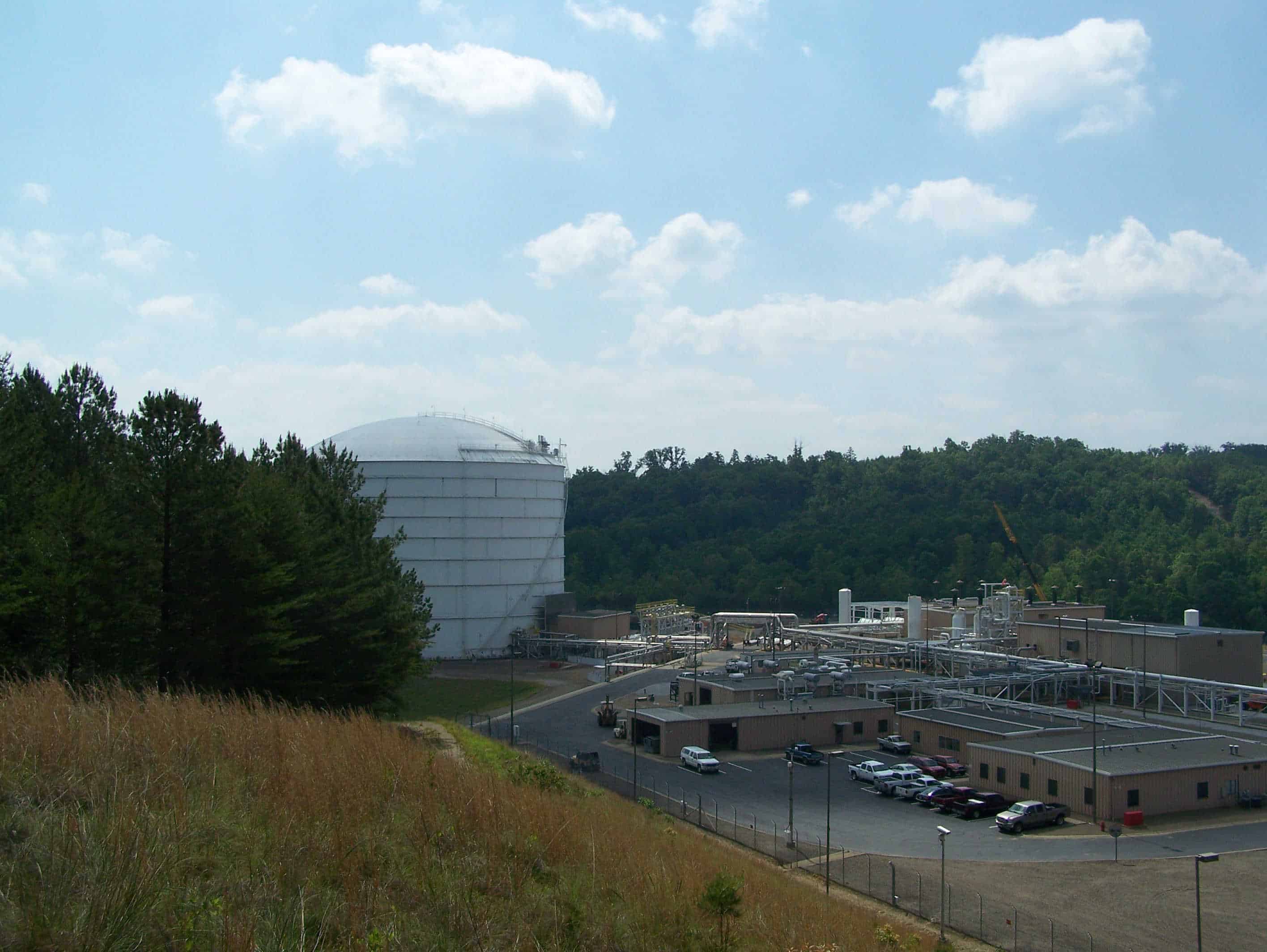
SIS has performed LNG peak shaving control systems for grass root projects, total facility system upgrades, liquefaction upgrades and system enhancements. This includes:
- HMI graphics
- IO testing and field commissioning support
- Process controls including:
- Boil off vapor compression control
- Liquefaction pretreatment control
- MRL loop control
- Vaporization and flow rate control
- Safety system monitoring and shutdown
Some locations that we have worked at include:
- Bentonville LNG – PNG
- Bushy Park LNG – SCANA
- Chattanooga LNG – AGL Resources
- Cherokee LNG – AGL Resources
- Huntersville LNG – PNG
- Jacksonville LNG – AGL Resources
- Kingsport LNG – EnBridge
- Macon LNG – AGL Resources
- Nashville LNG – PNG
- Riverdale LNG – AGL Resources
- Robeson LNG – PNG
- Salley LNG – SCANA
- Trussville LNG – AGL Resources
LNG Terminal Controls – Southern LNG
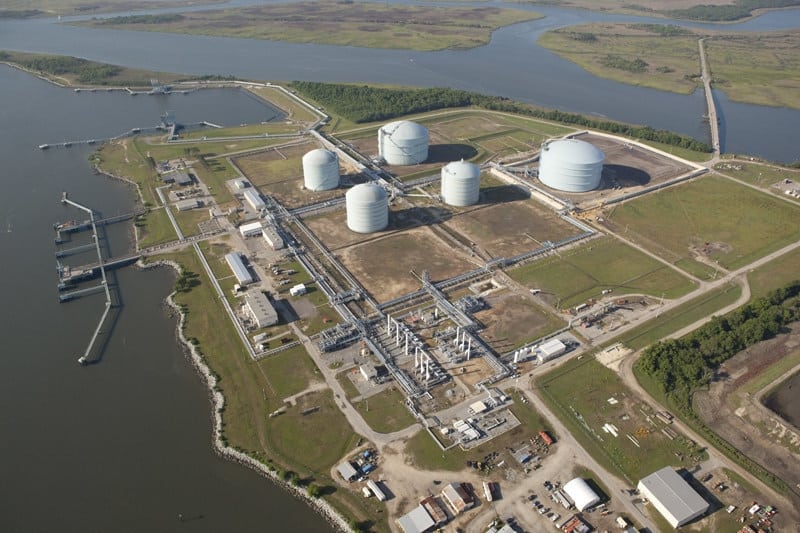
- Southern LNG’s Elba Island: After being idle for 20 years, SIS provided the following for the re-commissioning of the facility:
- Process controls including
- LNG tanker unloading
- LNG tank level and pressure control
- Booster, primary and secondary pump control
- Vaporization and flow rate control
- Boil off vapor compression control
- Safety system monitoring and shutdown
- Third-party communications including chromatographs, ship unloading arms, mooring tension systems and meter station RTUs.
- HMI graphics
- IO testing and field commissioning and training
- Process controls including
- Southern LNG’s Elba Island: For the train II and train III expansions, SIS provided:
- Process control software
- HMI graphics
- IO testing and field commissioning support for the train II and train III expansions.
- Gulf LNG: Field support for general maintenance and system enhancements.
Dehydration Facilities – Toca Dehy, Southern Natural Gas
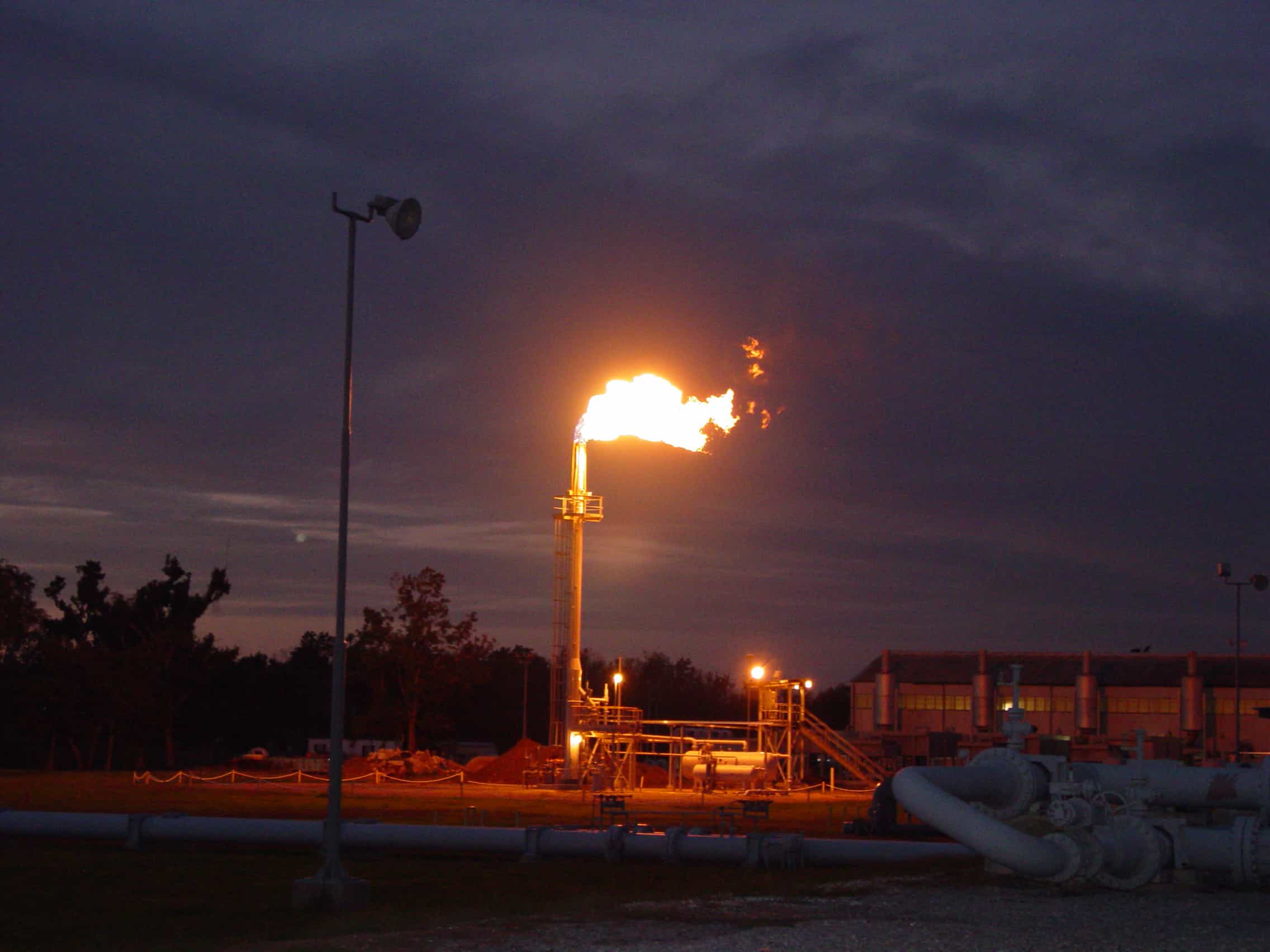
SIS has performed dry bed and glycol dehydration control systems for grass root projects, total facility system upgrades, and system enhancements. Control systems include:
- Tower sequencing
- Gas flow control
- Regeneration flow control
- Gas cooler control
- Regeneration heater control systems
- Safety monitoring.
Some locations that we have worked at include:- Bear Creek Storage – Southern Natural Gas
- Golden Triangle Storage – AGL Resources
- Jefferson Island Storage & Hub – AGL Resources
- Toca Dehy – Southern Natural Gas
Compressor Station Controls – Station 394, NGPL
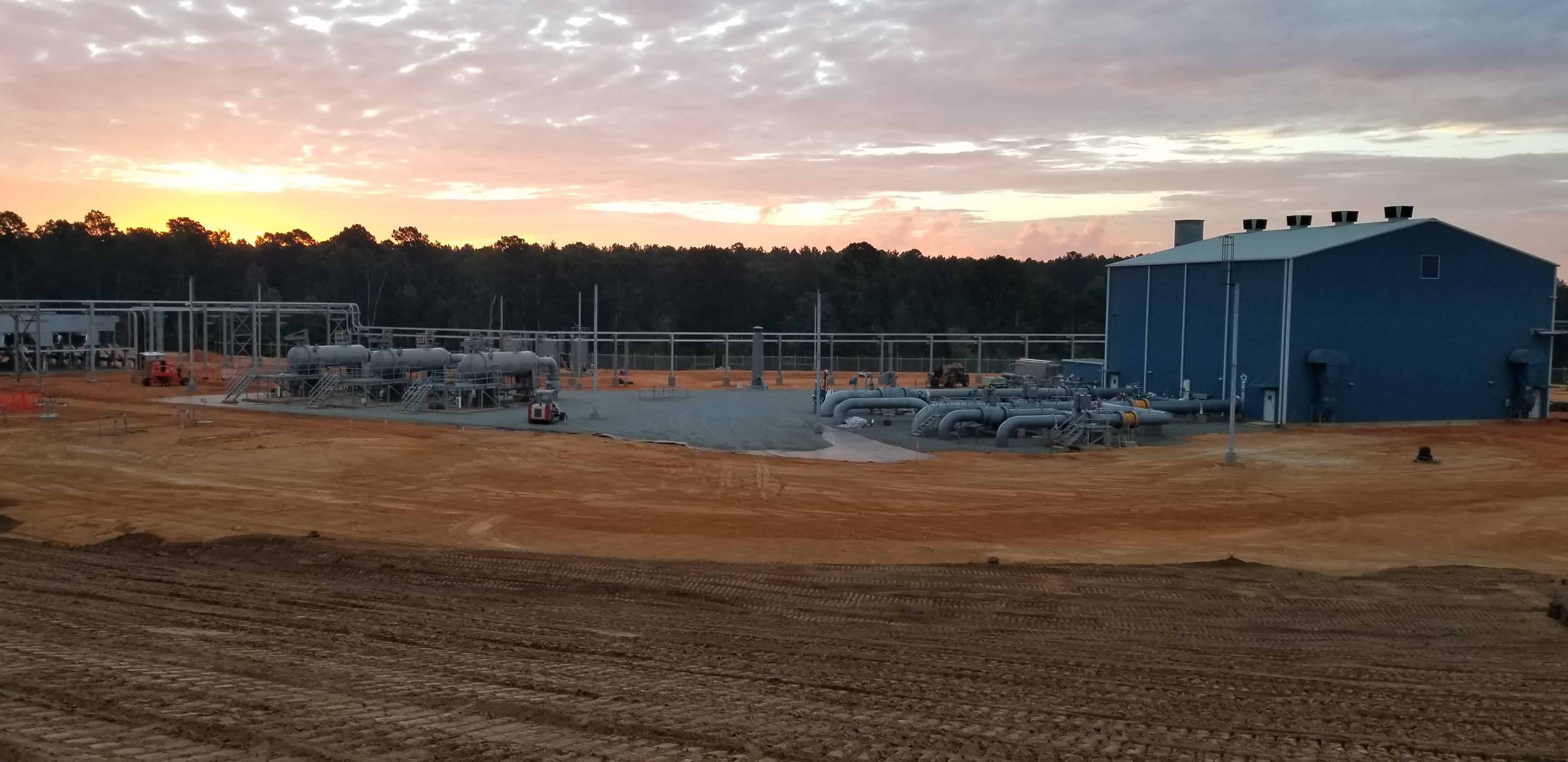
SIS has performed compressor station automation systems for grass root projects, total facility system upgrades, and system enhancements. Control systems include:
- Yard valve sequences
- Station set point control
- Gas cooling control
- Pressure, flow, temperature and level control
- Engineering calculations
- Safety system monitoring and shutdown control.
Some pipelines that we have worked on include:- AGL Resources
- ANR Pipeline
- Columbia Gas
- Destin Pipeline
- East Tennessee Natural Gas Pipeline
- Great Lakes Pipeline
- Natural Gas Pipeline
- Piedmont Natural Gas
- Sea Robin Pipeline
- Southern Natural Gas
- Tennessee Gas Pipeline
Gas Storage Facilities – Bear Creek Storage, Kinder Morgan
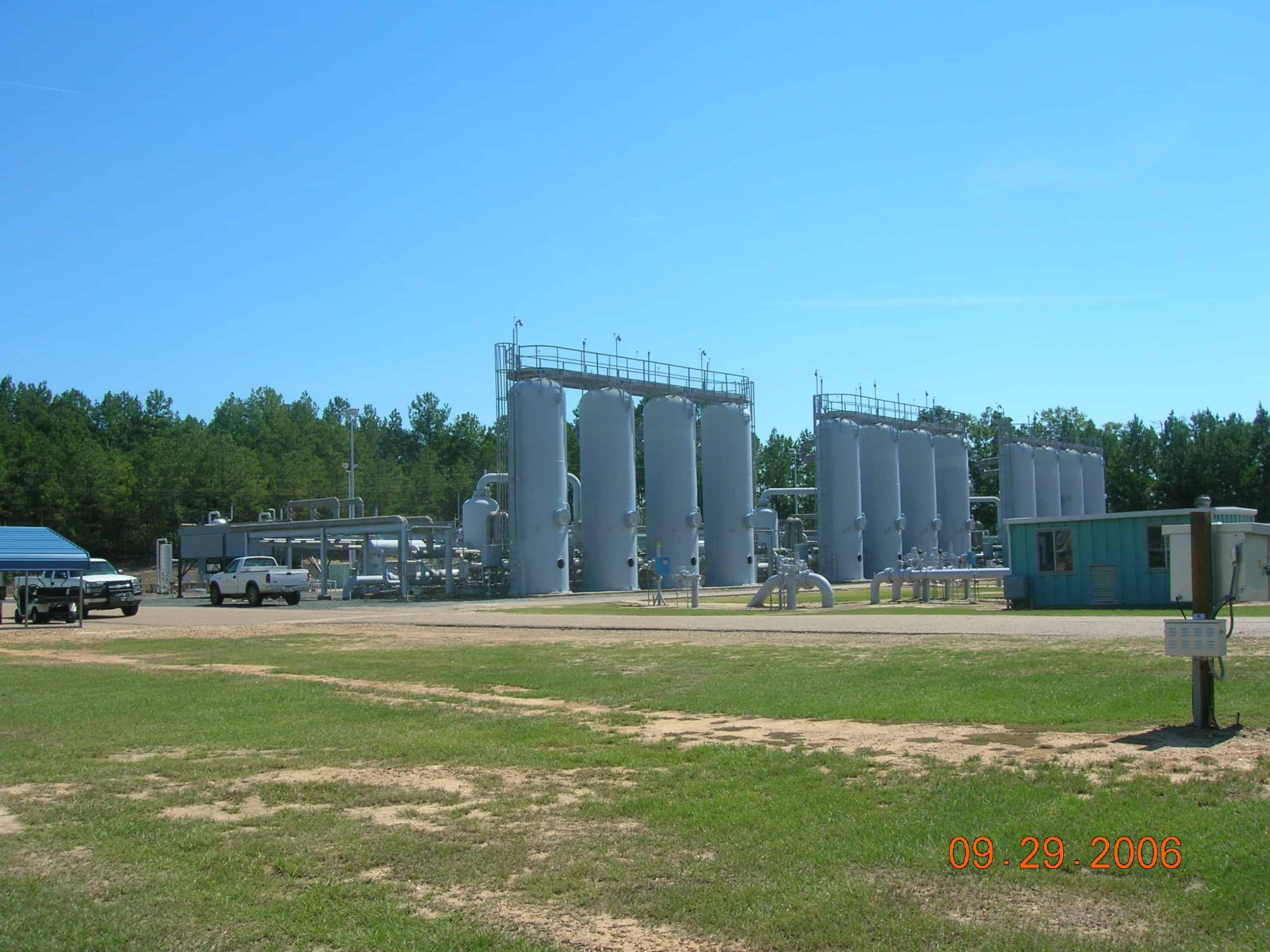
- Yard valve sequences
- Gas heater controls
- Flow and pressure controls
- Engineering calculations
- Safety system controls.
Some locations that we have worked at include:- Bear Creek Storage – Kinder Morgan
- Central Valley Gas & Storage – Pivotal Energy
- Coastal Caverns – Vitol
- Golden Triangle Storage – AGL Resources
- Jefferson Island Storage & Hub – AGL Resources
- Saltville Storage – EnBridge
Reciprocating Engine Controls
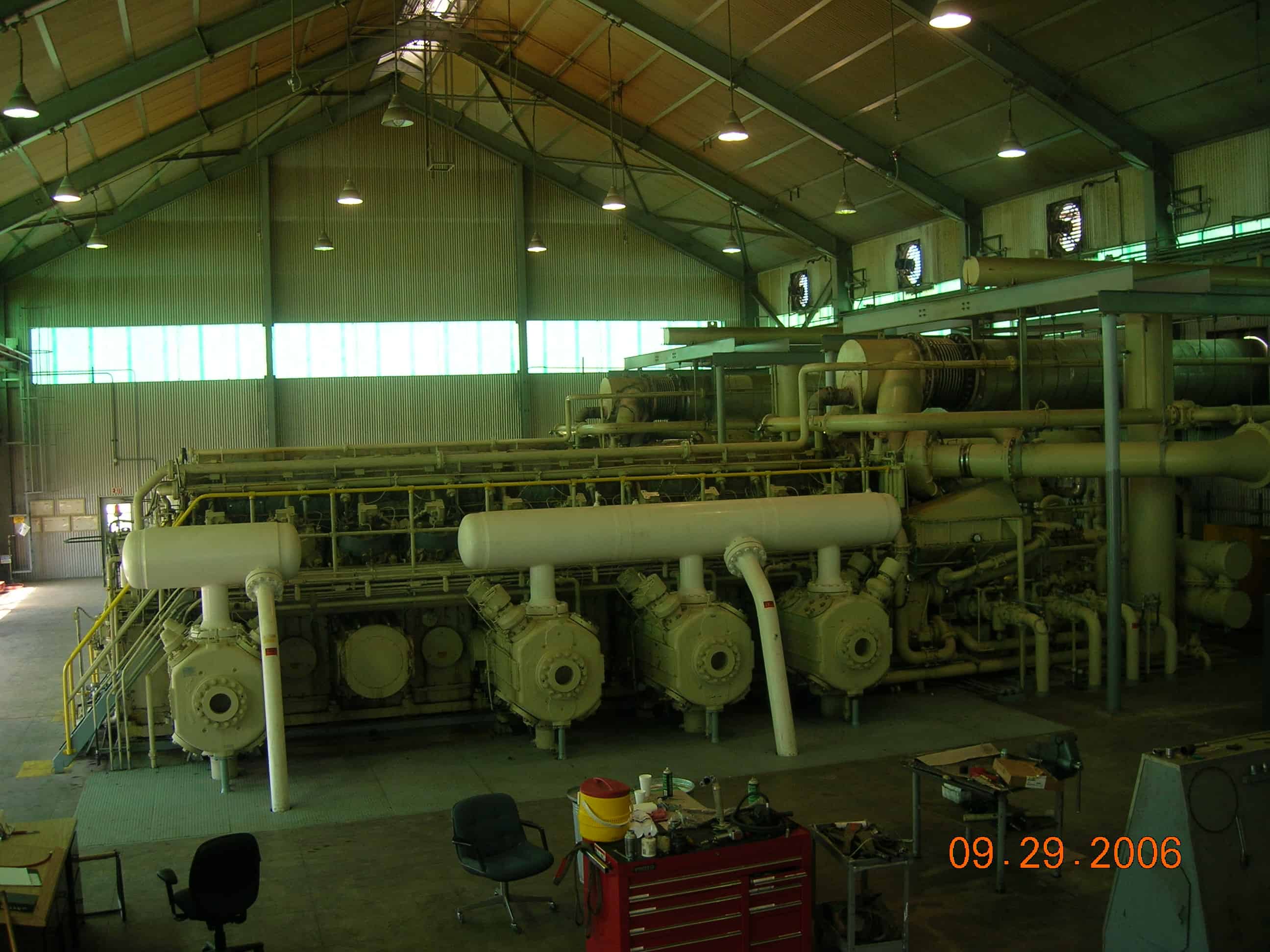
SIS has developed and implemented the following controls systems for reciprocating engines:
- Air-to-fuel ratio control
- Alarm & shutdown monitoring & control
- Engineering calculations for torque, capacity, horsepower, rod load, etc.
- First out counter messaging
- Governor speed control
- Historical run hours & volume logging
- Ignition timing control
- Jet assist air pressure control
- Power & compressor cylinder lube monitoring
- Torque/unloader control
- Unit start and stop sequencing
- Unit valve sequencing
- Water & oil temperature control
Oil Storage & Pumping Facility – Dickenson Station, Vitol
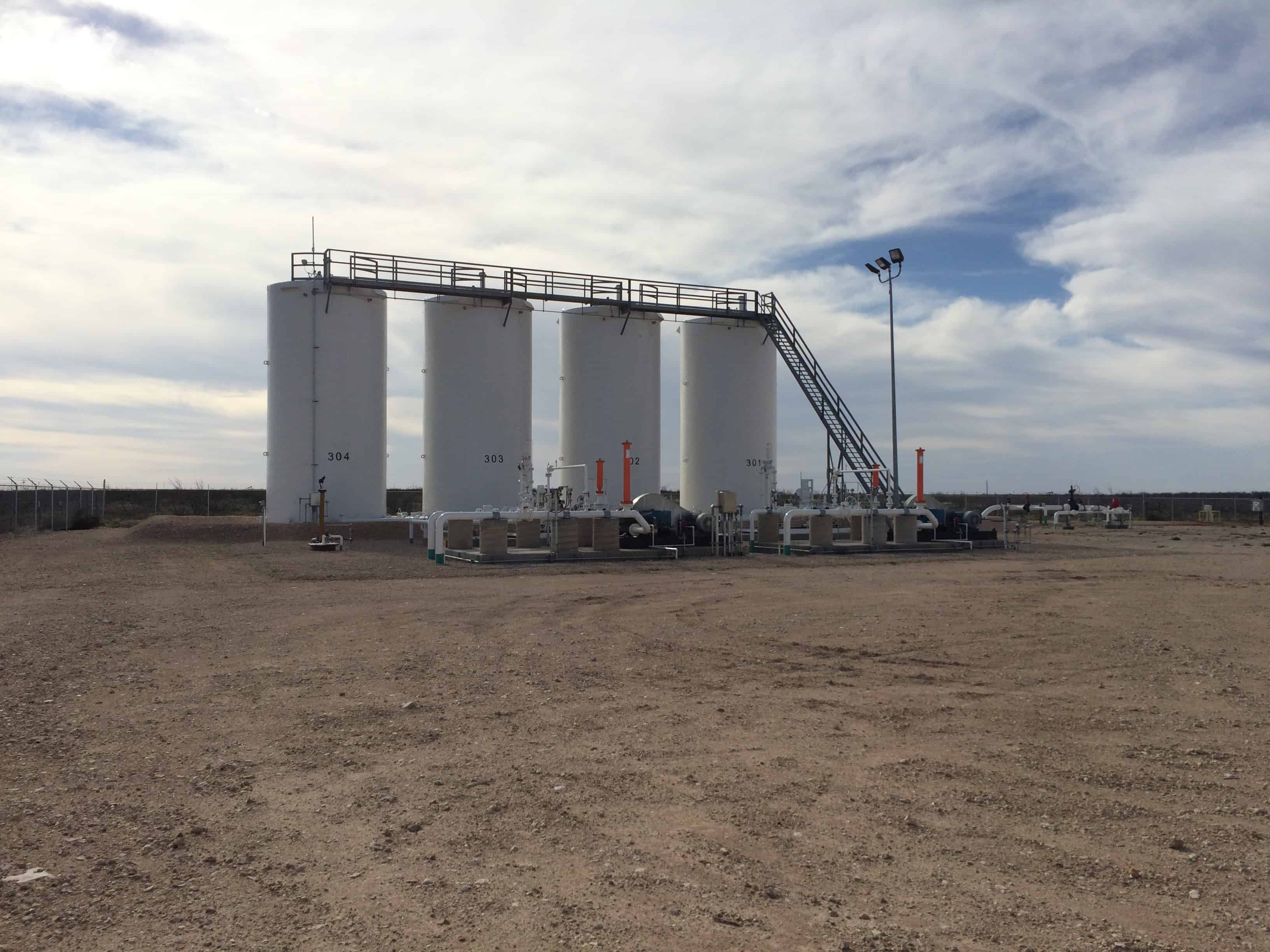
SIS has developed and implemented the following controls systems for oil storage and pumping facilities:
- Automatic valve sequencing
- Storage tank mixing & batching control
- Drag reducing agent (DRA) pump, tank and flow control
- Engineering calculations, flow rate, volumes, oil density, etc.
- LACT monitoring & controls systems
- Historical run hours & volume logging
- PD & centrifugal pump monitoring & control
- Pressure & flow rate control
- Safety system monitoring & control
- Storage tank level control
- Sump tank level control & system shutdown
- Tanker truck unloading monitoring & control